Organic fertilizer granulator machine: disc granulator, new organic fertilizer granulator, drum granulator, roller extrusion granulator and so on, the most commonly used granulation equipment is the above. In the production of organic fertilizer, the selection of granulator is usually decided by many factors, such as raw materials, output and price.
The new organic fertilizer granulator is a granulating equipment specialized in the production of organic fertilizer. It is also called an internal stirring tooth granulator. It is suitable for granulating materials with relatively large fibers. The shape of the finished product is oblate and needs to be processed by a rounding machine. It can be processed into a circle.
Both the drum granulator and the disc granulator belong to the agglomeration method.Compared with the disc granulator, the drum granulator relies on the temperature of the high granulation to increase the amount of liquid in the basic material, and promote the material to be more Balls are formed under low water content, which has the advantages of easy drying, energy saving and consumption reduction. But when the process conditions are not well controlled, the return material is high.
The roller extrusion granulator is a room temperature granulation equipment, which does not produce a large amount of dust and smoke when working, and it is suitable for a wide range of materials.
Price of organic fertilizer granulator machine:
1. If you want to buy granulator, no matter what kind of granulator you buy, it should be integrated according to the actual conditions.
2. Parameters of organic fertilizer pelletizer most businesses provide you with various parameters to facilitate your purchase.
3. There are many kinds of price of organic fertilizer granulator, and the merchants have made it clear on the price. Even if you don’t understand it, we can help you understand it clearly. A variety of fertilizer granulators produced by our company are available for you to choose.
In order to understand the fertilizer granulator machine price, we should first know what kind of fertilizer granules we want to produce, and then we should choose the appropriate fertilizer granulator according to our own production capacity.
Posts from November 2023
Roller granulator reduces dust and pollution during fertilizer processing
With the improvement of fertilization equipment, the granulated fertilizer is easy to store and transport. Fertilizer storage does not agglomerate. The drum granulator does not produce a large amount of dust and smoke when it is working, and it has a wide range of applicable materials. It can granulate materials that cannot be processed by other granulators, and has a high granulation rate.
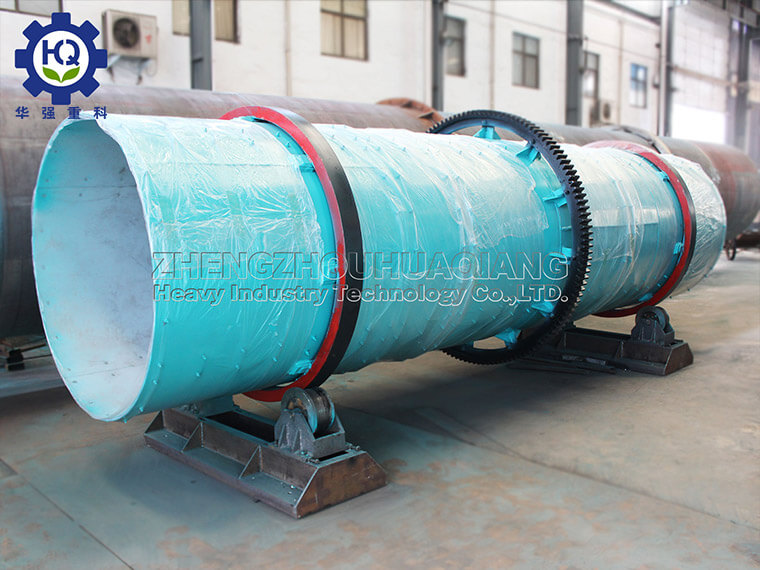
Features of drum granulator:
(1) The drum granulator is one of the key equipment in the compound fertilizer industry.
(2) It is suitable for hot and cold granulation of compound fertilizers and large-scale production of compound fertilizers with high, medium and low concentrations.
(3) The npk fertilizer granulator shell adopts special rubber plate lining or acid-resistant stainless steel lining plate. The raw materials are not easy to stick to the wall of the cylinder and play a role in corrosion protection. The drum granulator has large output, good economic efficiency and resource saving.
(4) The ball has high strength, good appearance, corrosion resistance, wear resistance, low energy consumption, long service life, and convenient operation and maintenance.
The drum granulator is suitable for large-span, high-depth fermentation and granulation of organic waste such as pig, sheep, cattle, chicken and other livestock manure, sludge garbage, sugar factory filter mud, slag cake, straw sawdust and other organic waste.
The working principle and advantages of an inorganic fertilizer composite fertilizer extrusion granulator
As a general organic fertilizer production, the steps mainly include crushing, fermentation, granulation, drying, and other steps. However, if you want to meet the local needs, you need to add a certain amount of N, P, K, and other composite fertilizers, then mix and stir evenly, and use physical extrusion to make particles.
The inorganic fertilizer composite fertilizer extrusion granulator is produced using a non drying room temperature process, with a production capacity of 1-1.5 tons/hour, 1.5-3 tons/hour, and other specifications. It can produce various concentrations and types of compound fertilizers (including organic fertilizers, inorganic fertilizers, biological fertilizers, magnetized fertilizers, etc.). This equipment has low investment and good economic benefits. The complete equipment layout is compact, scientific and reasonable, energy-saving and consumption reducing, stable operation, reliable operation, and convenient maintenance.
The working principle of the inorganic fertilizer composite fertilizer extrusion granulator is that the belt pulley is driven by an electric motor, and the transmission belt is transmitted to a pair of high-pressure roller bodies with sliding mold shells through a reducer for relative work.
The two rollers of the inorganic fertilizer compound fertilizer extrusion granulator are interacted with each other by a set of opposing gears. The two rollers of the extrusion granulator are directly driven by two output shafts on a dedicated reducer to achieve the purpose of extrusion molding. During production, the raw materials enter the feed hopper and are relatively extruded by the high-pressure roller body. After demolding, they flow to the lower part of the roller body for crushing and forming.
The granulation methods of different types of organic fertilizer granulators
Organic fertilizer granulator machine is used to granulate various organic wastes (straw, livestock manure, cake fertilizer, peat, etc.) after fermentation, and process them into spherical, rod-shaped or other amorphous particles. Compared with traditional farmyard manure, pelletized organic manure not only promotes the reuse of organic waste materials, but also has the characteristics of high permeability and high fertilizer efficiency, so it is more and more widely used.
The existing granulators of organic fertilizer not only need to adjust the formula of fertilizer, but also adjust the temperature and humidity, especially the temperature and humidity conditions are very critical to the formation of organic fertilizer. However, the existing organic fertilizer granulator machine generally ignore the influence of temperature and humidity on the formation of granulation, resulting in the phenomenon of organic fertilizer sticking, caking or moistening, mildew before leaving the factory, low product quality and high fertilizer efficiency It needs to be improved.
The output power of the organic fertilizer granulator machine is transmitted by the reducer through the transmission shaft, which drives the equipment to rotate as a whole. The front section is the forced feeding system, the back section is the internal stirring teeth, and the cylinder wall is lined with stainless steel. After the material enters, the stirring teeth force the material to form a ball. The ball forming rate is 100%, and the material moisture requirement is 25% – 45% It is not suitable to add too much humic acid, because humic acid will produce high temperature due to kneading, so that the material moisture is not balanced, which is easy to cause problems such as material not forming, equipment blocking and so on.
How to purchase a suitable new type of organic fertilizer granulator for aquaculture farms
The new type of organic fertilizer granulator machine is mainly used for the granulation of all kinds of organic materials after fermentation. It breaks through the conventional granulation process. Before granulation, the materials do not need to be dried. After crushing, the spherical particles can be processed directly. It saves energy and has higher pelleting rate. The content of organic matter is more than 97, so the granulation of pure organic matter can be realized without adding binder. The granule is solid and beautiful. After granulation, it can be sieved and thrown round to reduce drying energy consumption. The moisture content of raw material can be between 20-50.

During the inspection and purchase of organic fertilizer granulator machine, it is easy to be dazzled by some virtual websites, various advertisements and letters, or confused by the so-called low quotation, resulting in the purchase of inferior products, causing great losses. In order to ensure that you can purchase reliable products and rely on them for long-term use, the following suggestions are put forward for your reference:
1. Look at the production scale, product development technology, processing and manufacturing capacity of organic fertilizer granulator machine manufacturers.
2. It depends on whether the materials and parts are standard or not, on the processing and production technology, and on the product test results and measures.
3. How about after-sales service and technical ability.
Common fertilizer granulators used in the complete extrusion granulation production line of composite fertilizers
The complete set of compound fertilizer extrusion granulation fertilizer production line uses roller extrusion granulation machines for many fertilizers such as mixed fertilizer, compound fertilizer, ammonia fertilizer, and potassium fertilizer granulation. This machine has dual input shafts for granulation, and is a non drying granulation machine that integrates granulation, forming, and grading. Adopting room temperature granulation without drying system, forming in one go, with regular appearance, simple operation, and low energy consumption. Among the many fertilizer production line equipment used in potassium fertilizer, ammonia fertilizer, and mixed fertilizer granulation, it is a relatively cost-effective particle processing equipment.
The complete set of extrusion and granulation production line for compound fertilizers has a wide range of applicability for raw materials. It can not only be used for the processing of fertilizer particles, but also for the granulation of feed particles and chemical industries. It is also suitable for environmental protection engineering. Such widespread use reflects the high cost-effectiveness of roller extrusion granulators in fertilizer granulation equipment, which is relatively more cost-effective.
The complete set of extrusion and granulation production line for compound fertilizer is made of highly corrosion-resistant and wear-resistant materials. The roller skin of the roller extrusion and granulation machine has the advantages of beautiful appearance, simple operation, low energy consumption, long service life, and high granulation rate. It is a relatively advanced compound fertilizer granulation equipment in China, and its products are distributed throughout the country.
The complete set of compound fertilizer extrusion granulation fertilizer production line is not a fixed equipment as we imagine, but needs to be determined based on the on-site site and materials. The prices of the complete set of compound fertilizer extrusion granulation fertilizer production line vary with different yields.
Choosing an organic fertilizer granulator should pay attention to the type and purpose of the fertilizer
In recent years, the use of organic fertilizer granulator machine is more and more widely, and more and more customers buy it. Especially with the strong support of the state for the production of organic fertilizer, the sales of organic fertilizer granulator is hot, so what should we do when we buy granulator? In recent years, the use of organic fertilizer granulator is more and more widely, and more and more customers buy organic fertilizer granulator machine.
Organic fertilizer granulator is suitable for the granulation of light fine powder materials. The finer the basic particles of fine powder materials, the higher the sphericity of the particles, and the better the quality of the pellets. It is generally required that the particle size of materials before granulation should be less than 200 mesh. Typical application materials: chicken manure, pig manure, cow manure, tanli, clay, kaolin, etc.
It is special for granulation of organic fermentation fertilizer with municipal solid waste, such as raw material of organic fertilizer, livestock manure, manure, compost fertilizer, green manure, sea manure, cake fertilizer, peat, soil and miscellaneous fertilizer, three wastes, microorganism, etc. the particles are irregular pellets.
When customers buy organic fertilizer granulator machine, they must choose the manufacturer with certain technical strength and perfect after-sales service. Now there are many enterprises producing organic fertilizer granulator in China. Some enterprises have no technology at all, and they are completely imitating other manufacturers. The quality of organic fertilizer granulator is not up to standard, and some have no way to use it normally.
In order to make the equipment cheap, we must pay attention to the quality of the machinery itself, and find a professional manufacturer of the organic fertilizer granulator to cooperate. Only in this way can the customers completely avoid the worries of back-end, production at ease, and create greater wealth.
How to solve the problem of low particle formation rate in disc granulators
Disc granulator as an old machine, fertilizer granulator machine price concessions, experienced the test of a variety of materials, but any equipment will have advantages and disadvantages. With the diversification of raw materials, organic fertilizer equipment manufacturers are constantly developing new granulation equipment. Organic fertilizer granulator machine manufacturers help you solve the problem that the material is difficult to form in disc granulation.
In addition to the subjective factors of raw material composition, the particle forming of disc granulator is also closely related to the fineness of raw material, water content, the addition of auxiliary adhesive and the angle of disc operation. These problems should be constantly tried, according to their own material situation to achieve their own ratio, do some improvement, can achieve our expected value.

Characteristics of disc granulator in production line
1) The use of a unique combination of no power blade integration to reduce auxiliary power consumption.
2) The tilt angle of the large plate can be adjusted. The angle gasket is used for flexible and convenient adjustment.
3) The structure of disc granulator is novel and reasonable, and its weight and height are reduced.
4) The large plate is composed of plate body and plate section. Reduce the main motor power. The disc section can be adjusted up and down along the disc body.
5) When the feed ball is discharged, it can ensure that the feed ball will not be pulled or torn.
6) The whole organic fertilizer granulator machine is made up of non power combined blade for edge cleaning and bottom cleaning, angle cleaning blade for angle cleaning, combined with the unique treatment technology of plate body, with high pelletizing rate, no large mud mass, 90 degree ball diameter and 3-5mm particle size.
Equipment configuration and process of the 20000 ton organic fertilizer disc granulation production line
The 20000 ton organic fertilizer disc granulation production line disc granulator is a molding machine that can manufacture materials into specific shapes. Widely used in chemical, petrochemical, pharmaceutical, food, building materials, mining, environmental protection, printing and dyeing, ceramics, rubber, plastics and other fields. According to its structure and working principle, it can be further divided into disc granulators, rotary belt condensation granulators, flat twin screw extruders, rotary drum drying and slicing machines, roller dry granulation machines (referred to as roller dry granulation machines), toothed granulation machines, and disc vacuum condensation granulators. The use of disc granulators in mineral processing technology is mainly used for the production of low and medium content composite fertilizers, as well as for the granulation of organic, inorganic composite fertilizers and elemental fertilizers.
The disc granulator can be used for various dry powder granulation and wet granulation of dry powder. Wet granulation has a good effect and should be prioritized. It is the main equipment for pelletizing powder materials, with advantages such as uniform pelletizing, easy control of water content in the pellets, high strength of the pellets, simple structure, convenient control, low power consumption, and smooth operation.
The 20000 ton organic fertilizer disc granulation production line mainly consists of fermentation system, drying system, deodorization and dust removal system, crushing system, ingredient system, mixing system, granulation system, screening system, and finished product packaging system.
The disc type granulator adopts an overall circular arc structure, with a granulation rate of over 93. The granulator disc has three discharge ports, which are convenient for intermittent production operations, greatly reducing labor intensity and improving labor efficiency. The reducer and motor are driven by flexible belts, ensuring smooth starting, reducing impact force, and improving equipment service life. The bottom of the granulator disc is reinforced with multiple radiating steel plates, which are sturdy and durable, without deformation. The base design is thickened, weighted, and sturdy, Without the need for anchor bolts to fix, it operates smoothly and is an ideal equipment for granulating organic and compound fertilizers.
The Role of Binders in the Production of Fertilizer by Fertilizer Granulators
Binder refers to a substance that promotes the agglomeration of raw material powder and particles during the granulation process, improves the granulation efficiency, increases the yield, and improves the physical properties of the granules (strength, surface morphology, disintegration resistance, etc.). In wet granulation such as rotary drum granulator, disc granulator, and stirring granulator, granulating liquid such as water is added to the raw material powder to make the surface of the powder wet and form solid-liquid crosslinks. Reunite into pellets. On the other hand, in dry granulation, such as briquetting granulation and melt granulation, since the granulation is completed by intermolecular forces, there is no need to add a granulation binder.
The principle of drum granulation is that materials rely on surface tension, an appropriate amount of liquid phase, extrusion force generated by rolling between materials, and small particles are taken as the core in the correct movement direction of materials in the granulator to absorb large particles and adhere to small particles and form balls during rolling. The higher the rolling frequency in a certain time, the higher the balling rate and the rounder the particles are after forming.
The organic fertilizer rotary drum granulator used in small and medium-sized fertilizer plants is a rotating circular granulator with a diameter of 1.2 – 2.4m and a length of 3 – 6m. A material retaining ring is arranged at the feeding end and the middle part of the simplified body, and the tail is smooth. The middle retaining ring of the organic fertilizer drum granulator divides the simplified body into two areas, the front area is the mixing granulation area, and the rear area is the particle polishing area.
The granulation binder used in the fertilizer granulation process should have the following functions:a. Certain adhesion
b. High surface tension
c. High solid crosslinking strength after drying
d. Low cost
e. When mixed with chemical fertilizers, it is harmless to crops
f. Biodegradability of synthetic organic materials