The organic hypertrophy obtained by biological fermentation is mostly coarse powder or irregular small pieces, which is inconvenient to use, especially to machine seeding in large area. Making these organic fertilizers into spherical granular organic fertilizers is the key to promote the use of organic hypertrophy areas.
The coarse powder or irregular small pieces of organic fertilizer after biological fermentation are characterized by high moisture, loose and many fibers. The existing technologies for preparing spherical granular organic fertilizer from coarse powder or irregular small pieces of organic fertilizer after biological fermentation are mainly as follows:
1. Some manufacturers use the traditional disc fertilizer granulator or rotary drum granulator, need to dry and crush the coarse powder or irregular small pieces of organic fertilizer into very fine (more than 100 mesh) powder, and then add binder and inorganic fertilizer, and the amount of binder and inorganic fertilizer in organic fertilizer can not be more than 30%. Although this method can make spherical particles, due to processing The organic fertilizer in the process will be first crushed by sufficient precipitation, then granulated with water and then dried, repeated for many times, so the processing cost is quite high. Moreover, due to the low density of organic fertilizer, the particle strength is low, which is not conducive to storage, transportation and machine seeding;
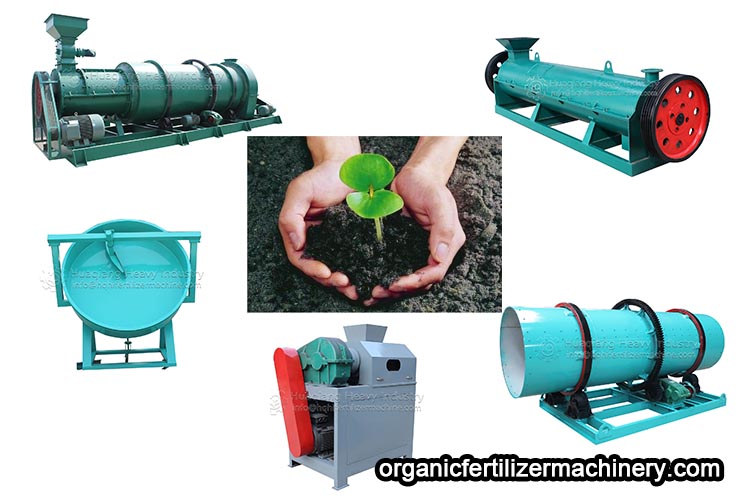
2. Some manufacturers first dry the organic fertilizer until the moisture content is only 20-25%, and then use the flat die extrusion granulator or the double roller granulator to extrude the dried organic fertilizer into columnar or flat spherical particles. Although this method is more convenient to use, it is not suitable for machine sowing, and it has poor appearance and poor sales;
3. Some manufacturers will first use the flat die extrusion granulator to extrude into short cylindrical particles (due to high moisture content and high fiber content, the columnar particles also have certain plasticity), then polish and shape them into spherical particles, and then dry, cool and screen the spherical particles to obtain qualified particles. In this method, raw materials do not need to be treated, the moisture sequence is reduced step by step, and the production cost is greatly reduced, However, there are some fatal weaknesses in this method, that is, organic fertilizer is easy to arch, block and bond, with small output and high power consumption in extrusion process.