Humic acid fertilizer refers to the production of a large amount of humic acid, nitrogen, phosphorus, potassium and some trace elements required by crop growth and development by using different production methods of peat, lignite and weathered coal. Humic acid, as the raw material of organic fertilizer production equipment, plays an important role in agricultural production, such as stimulating crop growth, improving soil, increasing nutrients and strengthening soil microbial activities.
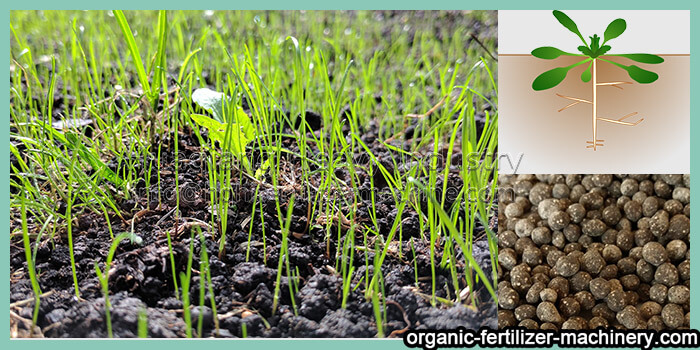
Varieties of humic acid fertilizer
1. Humic acid fertilizers can be divided into two categories: natural humic acid and artificial humic acid according to their sources. Among natural humic acids, they are divided into soil sodium humic acid (white) phytic acid, coal coal humic acid, Water humic acid and mold humic acid, etc. Humic acid can be made into solid particles by NPK fertilizer granulator.
2. Humic acid fertilizers can be divided into primary humic acid and regenerated humic acid (including humic acid in natural weathered coal and artificial oxidized coal) according to the production method.
3. Humic acid fertilizers can be classified into fulvic acid, brown fulvic acid and black fulvic acid according to their solubility and color in solvents. In the earlier literature, there were also names of grey fulvic acid, brown fulvic acid and green humic acid, which were actually separated from different solvents.
4. According to the natural binding state, humic acid fertilizer can be divided into free humic acid and (calcium, magnesium) combined humic acid. We provide humic acid processing equipment, disc granulator, grinder, dryer, etc.
5. Humic acid fertilizer can be divided into type A, type B (true humic acid), RP type and P type (immature humic acid) according to the humification degree of humic acid (such as absorption coefficient).