The dry granulation machine works without involving any liquids, including those binders and humectants such as water, alcohol, etc. Dry granulation mainly relies on the physical force of the machine to process the material. The enormous compaction or compression force provided causes the material particles to adhere to each other. Common organic fertilizer granulators include: roller extrusion granulator, rotary drum granulator, disc granulator, new organic fertilizer granulator, new two-in-one organic fertilizer granulator, flat die granulator machine, ring die pelletizer, Huaqiang Heavy Industry Technology’s dry-laid husk immediately can serve this purpose very well, these are double roller granulator and flat die granulator, they are of high quality, durability and reliability.
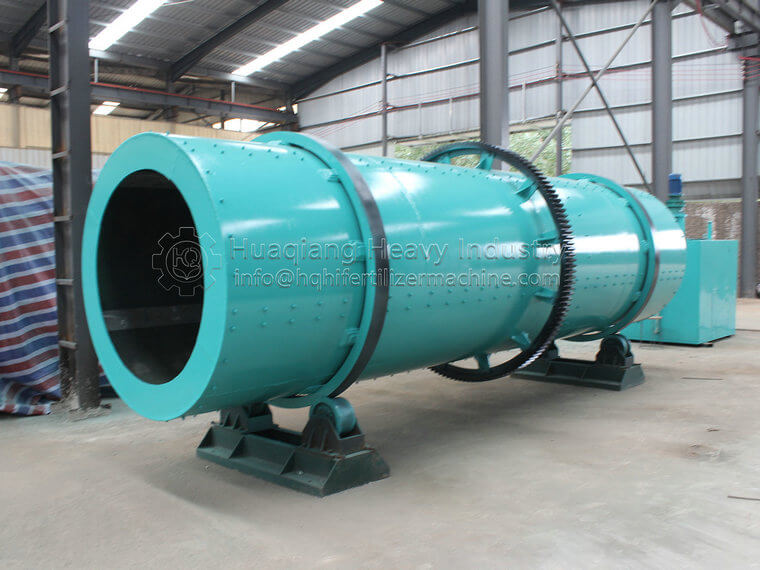
1. Fertilizer granulation
Since the dry granulator can improve work efficiency, reduce investment, and improve the nutritional value of granule products to a certain extent, it is widely used in the fertilizer granule manufacturing industry. You can use dry roller press or flat die granulator, organic fertilizer production line, npk production line, etc. at a lower cost.
2. Drug granulation
Dry granulation is important in the manufacture of certain tablets and capsules. It can save a lot of time and effort by making the process much simpler, so it is almost irreplaceable in the pharmaceutical industry. These tablets and capsules can be riboflavin, antibiotics, lactose, etc.
3. chemical granulation
Similar to pharmaceutical granulation, dry granulation is also important in the chemical industry. You can make some solid chemicals into pills or capsules using a twin-roller granulator.
4. Livestock feed pellets
Since the die of the flat die extrusion granulator can be replaced with different holes, you can use it to produce feed pellets of various sizes and shapes by dry granulation. These feeds are suitable for many farm animals such as chickens, ducks, pigs, cattle, sheep, rabbits, fish, etc.