The new fertilizer production line project should comprehensively consider the local resources, market capacity and market coverage radius. Generally, the annual output of small-scale new plants is 10000 tons (1.5 tons / hour), 20000 tons (3 tons / hour) and 30000 tons (4.5 tons / hour). The annual output of medium-sized factories is 50000-100000 tons, and that of large-scale factories is 100000-300000 tons.
The investment scale and scheme design need to be formulated according to the following conditions: characteristics of raw material resources, local soil conditions, local planting structure and main crop varieties, plant site conditions, selection of NPK fertilizer granulator, production automation degree, etc.
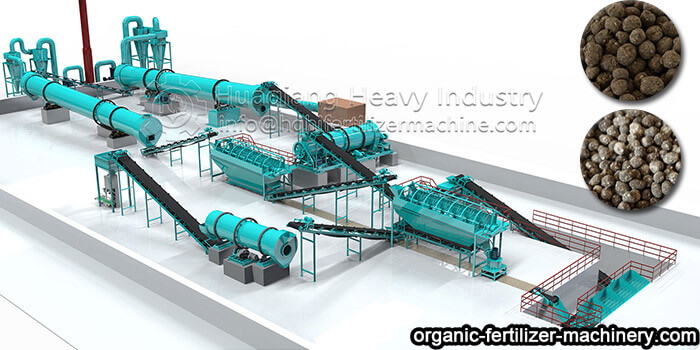
Several equipments of fertilizer production line
1. Mixer. In addition to chemical fertilizer raw materials, some sticky materials such as clay can be properly added during mixing. During operation, the materials are evenly mixed by stirring back and forth with multi-channel rotating blades.
2. Fertilizer granulator. Small scale production generally uses organic fertilizer granulator to meet the requirements.
3. The rotary dryer is mainly composed of drying cylinder, transmission device, supporting device, head and tail sealing parts. The diameter ranges from 80 cm to 3 m, and the length depends on the drying requirements. The dryer is a cylinder inclined to a certain angle with the horizontal direction. The material is added from the higher end, and the high-temperature flue gas and the material enter into the cylinder in parallel. With the rotation of the cylinder, the material moves to the lower end due to gravity. A lifting plate is welded on the inner wall of the cylinder to take up and drop the materials, and fully contact with hot air in the falling process, so as to achieve the purpose of drying.
4. The rotary cooler can reduce the moisture content while cooling a certain temperature. It is the same equipment as the dryer, except that the air is drawn from the head to the outside when used, so there is no need to seal the tail.
5. The drum screening machine adopts a combined screen, which is convenient for maintenance and replacement. The machine has a simple structure, convenient operation and stable operation.