Posts in the npk fertilizer production line category:
Model Selection of Organic Fertilizer Granulator
The difference in the selection of organic fertilizer granulator models lies in the selection of appropriate granulation methods according to the use requirements of materials. This is just a big general term. There are subdivisions and branches under it. It is mainly divided into dry method and wet method:
Dry process mainly refers to products with relatively low water content. Generally, water content below 10% is a zero limit. (There are also few materials that can reach 16%, for example, some materials only carry crystal water.) Most of the particles produced by dry granulation are irregular particles (for example, ordinary granular potassium fertilizer) or the more common shape is similar to small gravel. With the current industrial upgrading and increasingly strict environmental protection requirements in China, many chemicals and building materials need granulation.
The main index of wet granulation is the material with a water content of more than 20%. There are various equipment and methods for wet granulation. For example, disc granulation, drum granulation and spiral granulation have been carried forward many years ago, and have been greatly improved by increasing the use environment and processing requirements of different materials. For example, the particle size of relatively popular organic fertilizers over the years ranges from 1mm to 6mm. These methods were adopted.
Compared with wet granulation, dry granulation in organic fertilizer granulator consumes less energy, is more environmentally friendly, does not require drying, does not add water and binder, and does not change the properties of materials; Compared with wet granulation, these are also several advantages of dry granulation. It is more suitable for industrial production.
In another case, some materials require relatively small particle sizes. Products between dozens of meshes and 100 meshes can also be reduced by airflow, spray and rapid drying.
Equipment and technology of packaging machine in npk fertilizer production line
Fertilizer automatic packing machine
The reason of raw material precipitation during npk fertilizer granulation
When some compound fertilizer equipment production lines are processed by rotary drum granulator, they can dissolve the fertilizer into a certain proportion, but if the energy exceeds a certain amount, it will produce salt analysis and precipitate another substance.
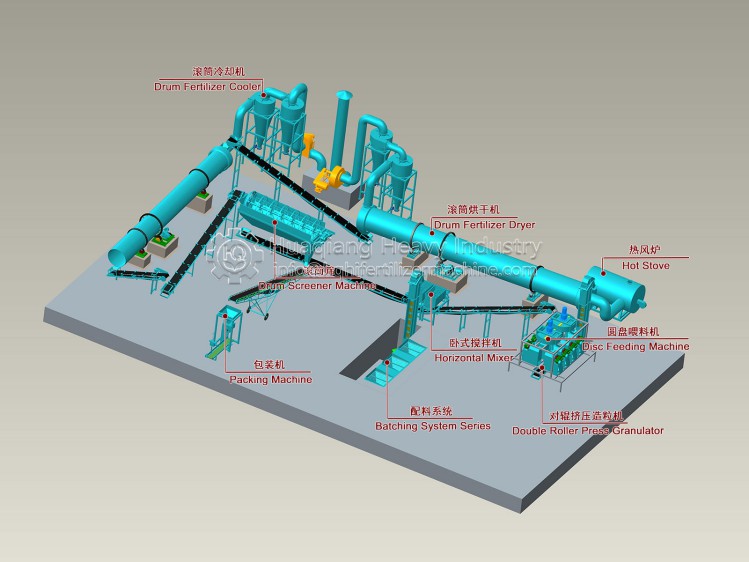
How to improve the granulation rate of drum granulator in organic fertilizer production line?
Producing the organic fertilizer granulator using the fertilizer granulator machine.Different type and model of organic fertilizer granulator machine can be used to produce the organic fertilizer granulator.How to improve the granulation rate of the rotary drum granulator?
In the fertilizer manufacturing process,the new type organic fertilizer drum granulator is a common granulator,which mainly uses high-temperature steam to make raw materials humidified to the granulation state.After the granulation of Huaqiang new type type organic fertilizer drum granulator,the particl temperature is very high.In the next drying process of organic fertilizer particles,the heat energy consumption of drying is saved,which is not efficient and engery-saving,and the granulation rate is up to more than 90%.
In order to improve the granulation rate of the new type organic fertilizer drum granulator in organic fertilizer production line,in addition to selecting a high-quality product,the granulation rate and output of the granulator can also be improve the granulation rate of new organic fertilizer drum granulator:
First,the time and frequency of material rolling in the new type of organic fertilizer drum granulator is the primary factory to determine the pelletilizing rate and particle roundness.The principle of rotating drum granulation is that the material depends on the surface tension,the appropriate liquid phase,the extrusion pressure generated by roller press which the roller press granulator machine is also to be designed and used in npk fertilizer manufacturing process in most of time,and correct movement direction of the material in the granulator is centered on small particles,which absorb and adhere to the ball in the rolling process.The higher the rolling frequency in a certain period of time,the higher the pelletilization rate is,and the rounder the particles will be after forming.In the process of production,we have encountered two situations due to the different friction between the material and the barrel wall of the granulator.
1.The internal surface finish of te granulator is large,which reduces the friction between the material and the cylinder wall,and weakens the upward movement force of the material.If the material does not roll,it will not produce particles.In view of this situation,we can solve it by adjusting the rotating speed of the new type of organic fertilizer drum granulator and installing a small-scale plate inside.
2.The material in the organic fertilizer drum granulator sticks to the walll seriously,the friction between the material in the granulator and the cylinder wall is enhanced,and the material in the granulator is lifted too high,which causes the material to be thrown down from the top,until the particles formed are not round and too many large particles.We think there are two reasons for this situation:on the one hand,there are too many stickly materials ,which we adopt.On other hand,the inside of the granulator is not smooth,which can be solved by changing the inside material and increasing the inside finish of the granulator.
The design of npk fertilizer production line by rotating drum granulation is that there is a steam pipe embeded in the feed bed,and a spray is arranged above the feed bed.Under the condition of stable production supply,the saturated steam provides part of water while providing heat,which increase the moisture content of the material.Through the use of steam,the temperature and viscosity of the material are increased,so that the moisture content of the mateiral can be reduced in the process of balling,thus reducing the drying load, and the liquid phase distribution of adding steam can be more uniform than adding water. Only when the liquid phase of the material is insufficient and the material is unstable, can the water be added as a supplementary means. In the process of production, we have encountered that because of the unreasonable installation of the steam nozzle and the uneven distribution of the liquid phase of the materials, the places where there are many liquid phases of the materials are stuck into a big ball, and the places where the liquid phase is insufficient, the materials are difficult to form a ball, which affects the formation of the particles. In view of this situation, we can increase the steam nozzle to improve the steam receiving area of materials.
In conclusion,in order to improve the granulation rate of the new type organic fertilizer drum granulator,it is necessary to stickly control the water content,carry out the water ratio according to the provisions of the fertilizer equipment manufacturer,and pay attention to the methods in the production process at ordinary times,so as to improve the granulation rate and output of the new type organic fertilizer drum granulator.
Mixing equipment in NPK fertilizer production process
In NPK production line, blender will be used to mix materials. Here is a brief introduction of screw blender.
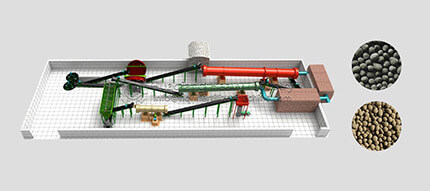
Structure of screw mixer
How to improve the pelletizing rate of NPK fertilizer production
NPK compound fertilizer is characterized by simple composition, high nutrient content, low dosage, quick fertilizer effect, convenient application, transportation and storage, and rapid improvement of yield and quality. In order to produce large quantities of high-quality compound fertilizer, the first step is to produce good fertilizer granules.
The main factors influencing NPK fertilizer production line are as follows:
- Production equipment;
- Process technology;
- Physical and chemical properties of raw materials;
- Production formula and added conditioner;
- Air temperature and air volume at the outlet of the dryer;
- Temperature and liquid phase quantity of granulating materials;
- Material flow;
- Material return ratio;
- Quality of operators;
- Climatic conditions.
Only by integrating the above factors into making fertilizer granules, can we produce NPK fertilizer with high yield and good quality, one of which is indispensable.
1. Improving the performance of NPK fertilizer production equipment is the basis
Choose qualified production equipment, choose well-equipped, complete test means, reliable product quality manufacturers, under the guidance of experienced personnel to buy, late equipment management and maintenance personnel to have a certain professional level. Zhengzhou Huaqiang Co.Ltd are leading agricultural fertilizer machine manufacturer in China. We has strong technical strength in fertilizer machines. All of our products comply with international quality standards and greatly appreciated in a variety of different markets throught the world.
2. Choosing ammonium phosphate with good viscosity as raw material is the premise
The pelletization of NPK fertilizer mainly depends on the viscosity of ammonium phosphate and conditioner, and the poor viscosity of ammonium phosphate directly affects the pelletization rate of compound fertilizer. Therefore, when purchasing ammonium phosphate, we should consider not only nutrient content and price, but also its viscosity. From the actual production experience, the viscosity of diammonium phosphate is better than that of monoammonium phosphate.
3. Ensuring the fineness of raw materials and feedbacks is essential
The finer the powder of the raw material, the better the viscosity of the material, the more important it is to improve the efficiency of the crusher
Chain crusher to help make the big granules into the fine powder and get back to fertilizer granulator machine. It is simple and compact in structure, cover small area, easy maintenance such characters, crushing effect is good, smooth operation, easy to clean.
4. Material mixing is an important measure to improve the NPK fertilizer production line efficiency
The material is mixed evenly, on the one hand, the mixer mixes the fresh material evenly, on the other hand, the mixer combines the returned material and the fresh material evenly. Because the fine powder in the returned material is mostly potassium and nitrogen with poor viscosity, it is the material that is least likely to form into a ball, while the fresh material has better viscosity and is easy to form into a large ball in production. Mix the two thoroughly to prevent the formation of large balls and too much powder.
5. Suitable moisture and pelletizing temperature are the key
Only when the temperature and water content of granulating materials are adjusted to the optimal point can the granulation area be ensured to be normal.
The disc fertilizer granulator is suitable for the production with small yield, and the rotary drum granulator is suitable for the mass production of NPK fertilizer. Addition of moisture during granulation requires certain experience of operators.
6. Suitable air volume and stable furnace temperature are the preconditions
The size of the air volume directly affects the drying effect, the air volume in the dryer, the drying effect is good. If the air volume is too large, it is easy to extract the powder in the simplified body, and the wind speed should be less than 2m/s. Best cooling head end temperature difference is about 100℃, the import and export temperature cannot frequent adjustment. When urea is used as nitrogen source, the temperature should be determined according to the amount of urea. The more urea is used, the lower the drying operation temperature will be.
NPK fertilizer manufacturing production process
In this article,brief introduction of complete equipment and process of compound fertilizer production line of Zhengzhou Huaqiang Heavy Industry Technology Co.Ltd.The npk fertilizer manufacturing process production of compound fertilizer is the general process of compound fertilizer production,which is of great significance for users to incest and fully understand the production of compound fertilizer.
The fertilizer manufacturing process of npk,compound fertilizer is roughly as follows:raw material proportioning,mixing,and stirring,agglomeration and crushing,material granulation,primary screening,particle drying,particle cooling,secondary grading of particles,coating of finished particles,quantitative packaging of finished particles,etc.
The following is a detailed introduction to each link of the production process of npk, compound fertilizer and in different producing parts it is equipped with different type fertilizer equipment:
The production process of npk,compound fertilizer includes raw material promoting,mixing,crushing and agglomeration,granulation,primary screening,particle,drying,particle cooling,secondary screening,particle coating of finished products and quantitative packaging of finished products.
1.Raw materia ingredients:generally the raw materials can be the urea,ammonium nitrate,ammonium chloride,ammonium sulfate,potassium chloride and other raw materials can be selected and prepared in a certain proportion.
2.Mixing parts:Minx the prepared raw materials evenly to improve the overall uniform fertilizer efficiency content of the fertilizer particles,and use the horizontal mixer or disc mixer to mix the raw materials.
3.Agglomerate crushing:the raw materials with uniform mixture are crushed to facilitate the subsequent granulation processing,mainly using chain crusher,etc.
4.Material granulation:evenly stirred and crushed materials are sent to the granulator by belt conveyor for fertilizer granulator machine(drum granulator,disc granulator and roller press granulator can be used),which is an essential and most important step in the production process of compound fertilizer.
5.Primary screening:preliminary screening of semi-finished particles.Unqualified particles are returned to the mixing and mining link for reprocessing.Generally,roller screener is used to sceeen the granulator.
6.Particle drying:the particles made by the granulator and screned by the first stage are sent to the dryer to dry the moisture contained in the particles,so as to increase the particle strength and facilitate the storage.Generally,the rotary dryer is used in the fertilizer manufacturing process.Sometimes,the series of fertilizer dryer is also equipped in the organic fertilizer production line.
7.Particle cooling:the dried fertilizer particles are easy to agglomerate due to their high temperature.After cooling,they are easy yo be stored and transported in bags and stored by a cooler.
8.Secondary grading of particles:The cooled particles are graded,the unqualified particles are crushed and regranulated,and the qualified products are screened out,which can be screened by the secondary drum screener machine.
9.Finsihed paticle coating:coating the qualified products to increase the brightness and roundness of the particles,so as to make the appearance more beautiful.Generally,the coating machine is used for coating.
10.Quantitative packaging of finished particles:the coated particles,which is to easy,the finished particles are sent to the silo by the belt conveyor for temporary srotage,and then connected to the electronic quantitative packaging scale,sewing machine and other automatic quantitative packaging and sealing bags,placed in the ventilation place for storage,so as to realize full automation.
Then production process of compound fertilizer is simple,the production process of npk, compound fertilizer production line is small,the floor area is small,the operation is simple,and the technical requirements are not high.
How to maintain fertilizer manufacturing equipment
Fertilizer equipment is an important tools for fertilizer manufacturing process. Fertilizers processed by fertilizer equipment have abundant and diverse nutrients, which are rich in materials needed by vegetation and can meet the needs of various nutrients for crop growth. After fertilizer equipment is put into production, attention should also be paid to maintenance and maintenance, not just production. Running the equipment according to usage standard to produce fertilizer, check regularly to ensure normal operation, so that the service life of the equipment is longer. Following are some techniques for maintaining fertilizer equipment.
- Bearings in fertilizer production equipment bear all the loads of the machine, so good lubrication has a great relationship with bearing life. The use of bearings affects the service life and operation rate of the machine. Therefore, it is recommended that bearings be inspected once every 7 days and lubricating oil be injected into them regularly.
- Check the machine of the whole fertilizer production line regularly, and pay attention to whether the work of each part of the fertilizer granulator machineis normal. The wear level of vulnerable parts should be checked, such as cleaning the chain every 3 days, and replacing the worn parts in time.
- If there is a fault in the running of the rotating gear, stop immediately to check and eliminate it.
- The chassis of fertilizer production equipment should be placed smoothly to remove dust and other impurities, so as to avoid special circumstances and serious accidents in the production of machinery.
It is suggested that fertilizer factories should do the following for fertilizer manufacturing process:
1) Improve the maintenance system and eliminate hidden dangers. When the fertilizer production line is put into production, it is necessary to formulate rules for the use of various machines and maintenance systems. Operators can operate and maintain according to the regulations, so as to prevent safety accidents and avoid unnecessary failures of machines. For example, when workers clean and maintain the machine, they can find out the problems existing in the machine and check them in time to avoid greater losses.
2) Maintenance of the machine should be carefully and in place. Whether the NPK fertilizer production process can operate efficiently and normally and give full play to its performance is not only related to the quality of the equipment itself, but also to the correct use and proper maintenance of the operators. Maintenance of the machine is troublesome, but if not done, it will affect the production of equipment products, maintenance costs and replacement costs of vulnerable parts will continue to increase.
3) It is necessary to assign responsibility, check and record every day, lubricate and maintain the important parts of the equipment (vulnerable parts, motors, reducers, bearings, etc.) according to the instructions before leaving work every day. If there is any damage, it should be replaced or repaired in time to avoid affecting the normal production the next day.
4) The cause of equipment failure should be analyzed in time and lessons learned. The reason for the failure of fertilizer equipment may be the failure of the machine itself, or the improper operation and maintenance, etc. Once the fertilizer equipment fails, we should analyze the causes of the problems, take measures to learn lessons and prevent similar situations from happening again.
Production process of potassium chloride by disc granulator machine
In the production of potassium chloride granular fertilizer, fertilizer granulator can be used to granulate powder. The particles produced by disc granulator are spherical and have good strength, which can be widely used in agricultural production.
In the granulation process of disc pan granulator, it is necessary to add a binder to make the granules shape. Binder can be compounded by common inorganic minerals in a certain proportion. Binder has synergistic effect when potassium chloride is pelleted. The effect of pelletizing rate and particle strength is good when the binder is used for pelletizing. Potassium chloride was granulated by disc pan granulator machine, and the granules were spherical.
NPK Fertilizer Production Line
NPK fertilizer production line deals with potassium chloride fertilizer. First, all raw materials are mixed by the batching system, and the material is crushed by chain mill to the appropriate size. The disc granulator makes the powder into granules. After drying and cooling, the granules of potassium chloride are coated with protective film by the fertilizer coating machine to complete the granular processing of potassium chloride.
When applying potassium chloride, attention should be paid to the appropriate period of potassium application. Generally, the application period of potassium fertilizer should be early or not late, and should be used as base fertilizer and early recovery period. When the application amount of potassium fertilizer is less, it can be used as base fertilizer once, and when the application amount of potassium fertilizer is more or the soil texture is lighter, the application effect is better divided into base fertilizer and topdressing fertilizer. Soil nutrients and fertilization status should also be taken into account in determining the suitable application period of potassium fertilizer. In severe potassium deficiency soils, all potassium fertilizers should be used as base fertilizers in medium soil potassium supply, and suitable organic fertilizers should be applied as base fertilizers, combined with topdressing.
Note the method of application of potassium chloride. The concentrated application of potassium fertilizer is beneficial to improve its utilization rate and obtain better results. However, it is not advisable to have direct contact with seeds or seedlings. For general crops, a combination of soil fertilization and foliar fertilization can be used.