The process of the drum type npk fertilizer granulator is based on monomer basic fertilizers such as: urea, ammonium nitrate, ammonium chloride, ammonium sulfate, ammonium phosphate (monoammonium phosphate, diammonium phosphate, heavy calcium, ordinary calcium), potassium chloride (Potassium sulfate) etc. as raw materials. After being crushed to a certain degree of fineness, the materials are agglomerated and granulated by humidification and heating in the rolling bed of the drum granulator. During the granulation process, it can also be rotated if conditions permit. The drum npk fertilizer granulator adds a small amount of phosphoric acid and ammonia to improve the granulation conditions.
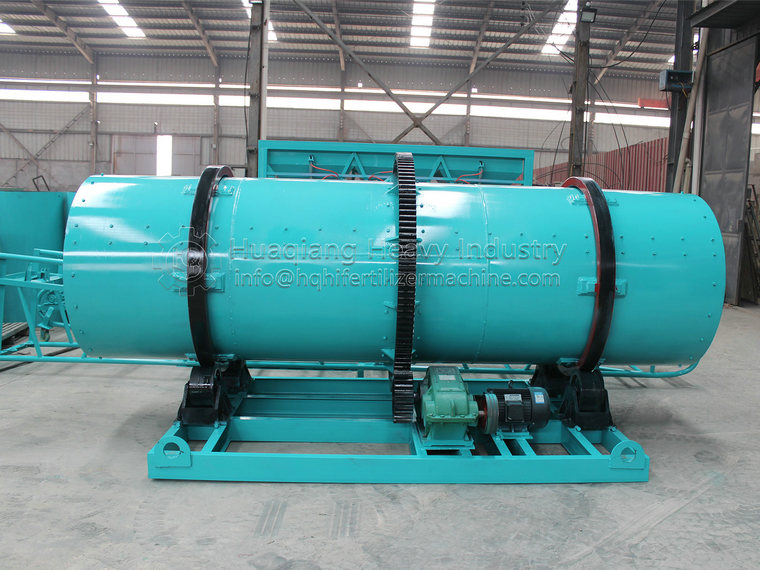
Process principle of drum type NPK fertilizer granulator
The material forms a rolling bed with the help of the friction generated by the rotation of the drum granulator. The extrusion force generated by the rolling makes the material with a certain liquid phase agglomerate into small particles. These small particles become the core and adhere to the surrounding powder to form larger particles. As the drum granulator is generally inclined to the discharge end of 1 °~ two point five °, Therefore, when the granular material rotates with the cylinder, it slowly rolls to the discharge port along the inclined direction of the cylinder. After leaving the drum granulator, the qualified granules are dried in the dryer, and then screened, cooled, coated, packaged and stored. After crushing, the material on the screen and the material under the screen will be sent to the hopper as the return material and granulated together with the basic fertilizer.
Process characteristics of drum type NPK fertilizer granulator
1. When the moisture content of the material is between 30% and 40%, it can be granulated, and the moisture content of the discharge material is about 30%, which reduces the traditional drying requirement of 70% moisture content and effectively reduces the production cost of organic fertilizer.
2. In the process of granulation, the temperature of 50 ~ 65 ℃ is produced in the cylinder, which reduces the moisture content of the discharged pellets by 5 ~ 8 points, thus reducing the drying cost.
3. The granulation particles are uniform, smooth, round, high strength, and the molding rate of particles is more than 95%.
4. By adjusting the water content of the feed, the size of the discharged pellets can be adjusted to meet the requirements of different pellet sizes.