Compared with chemical fertilizers, bio-organic fertilizers have a higher content of organic matter and are especially suitable for soil reclamation and soil improvement. Bio-organic fertilizers have a wide range of applications, including various food crops, cash crops, organic farms, etc. The demand for bio-organic fertilizers is higher, and the food and vegetables produced by bio-organic fertilizers taste better. After turning the waste from livestock and poultry breeding into organic fertilizer, it can generally be sold for 600-800 RMB/t.
Common organic fertilizer granulators on the market include: double-roll extrusion granulator, stock transfer granulator, disc granulator machine, new organic fertilizer granulator, new two-in-one organic fertilizer granulator, flat die granulator, ring die granulator, all kinds of granulators have their own production characteristics, and the fertilizer granulator machine price vary.
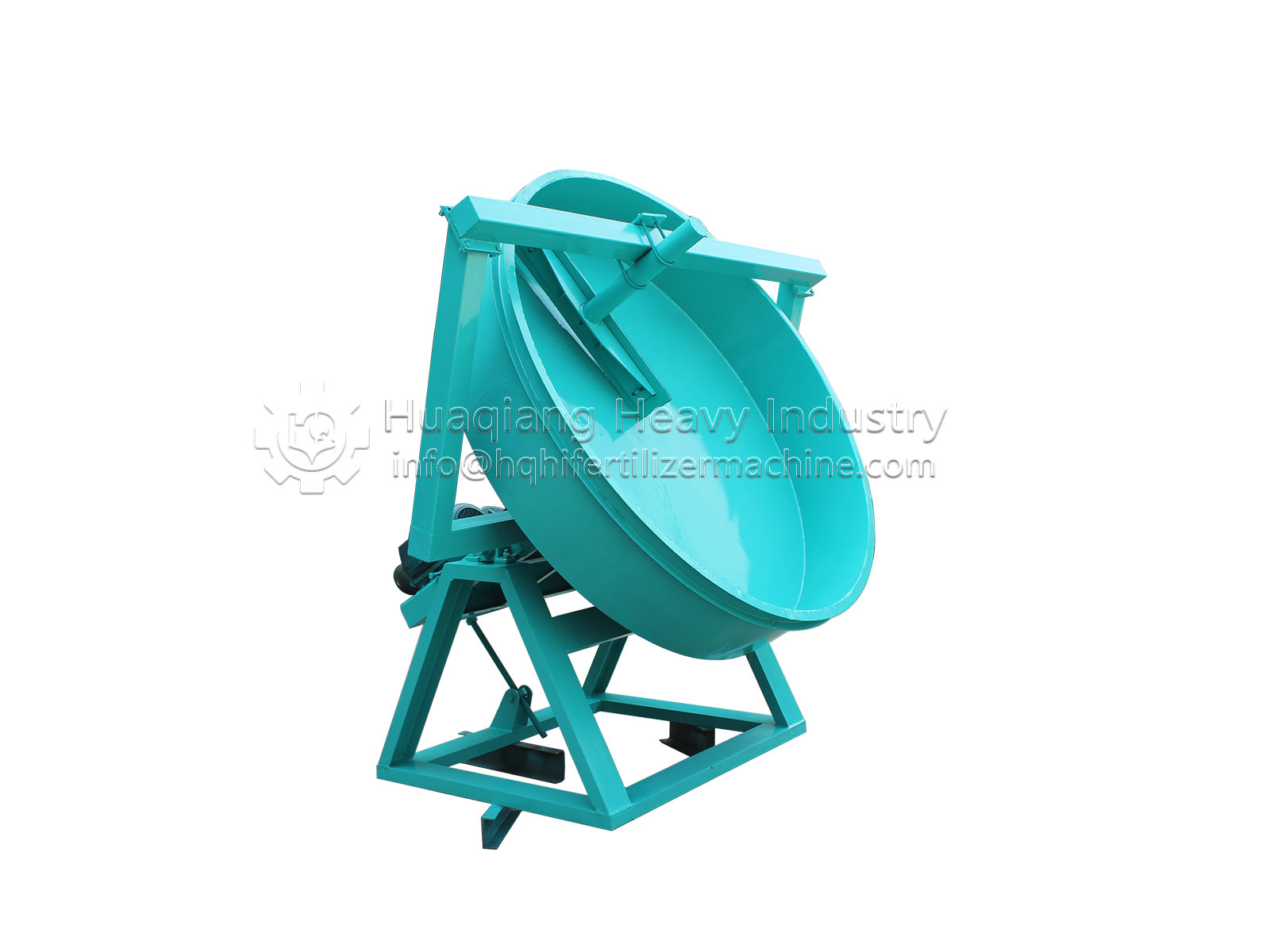
Stirring teeth organic fertilizer granulator is one of the key equipment in the organic fertilizer industry, suitable for cold and hot granulation and wide production of high, medium and low concentration compound fertilizers. The important working method is wet granulation, which undergoes unavoidable water or steam, so that the base fertilizer has rich chemical feedback after the cylinder is wet, and under the premise of the unavoidable liquid phase, with the help of the twisting action of the cylinder, the material is made The extrusion force between the particles agglomerates into balls. Cylinder accepts special rubber sheet lining or acid-resistant stainless steel lining, invalid ancient scraper assembly.
The npk fertilizer granulator is an improved product that absorbs the new technology of the international granulator. The machine is equipped with a feeding system connected with a pre-feeder and a forced-feeding screw feeding hopper that is assembled with the machine to ensure the continuity, richness and symmetry of the feeding, which is a crucial step. Uniform arc grooves are engraved on the paired rollers, which is conducive to material biting into the rollers, resulting in arc grooves sealing the cavity (belt), and also conducive to material compaction, reducing the forming pressure of the mechanism and the load of the main machine, and improving the manufacturing rate of the rollers.